上海鼎徵儀器儀表設備有限公司
ISO14993金屬和合金的腐蝕.在鹽霧、干燥和潮濕條件下循環暴露的加速試驗
ISO14993金屬和合金鹽霧/干燥/濕度循環腐蝕箱
Corrosion of metals and alloys — Accelerated testing
involving cyclic exposure to salt mist, dry and wet
conditions
WARNING — This document may involve hazardous materials, operations and equipment. It does
not purport to address all of the safety problems associated with its use. It is the responsibility
of the user of this document to establish appropriate safety and health practices.
1 Scope
This document specifies the apparatus and test procedure to be used in conducting accelerated
corrosion tests for the comparative evaluation of metallic materials with or without permanent
corrosion protection or temporary corrosion protection in salt-contaminated outdoor environments.
The test involves cyclic exposure of the specimens to neutral salt mist, “dry” and “wet” conditions. The
type of test specimen and the exposure period are not specified.
The particular advantages of this test over common accelerated tests such as the neutral salt spray
(NSS) test lie in its ability to better reproduce the corrosion that occurs in outdoor salt-contaminated
environments.
This document is applicable to
—
metals and their alloys,
—
metallic coatings (anodic and cathodic),
—
conversion coatings,
—
anodic oxide coatings, and
—
organic coatings on metallic materials.
NOTE
Methods of test for coatings to determine their resistance, in the presence of scribe marks through
to the substrate, to various cyclic corrosion conditions which include the condensation of water on the test
specimens during periods of humidity are given in ISO 11997-1.
2 Normative references
The following documents are referred to in the text in such a way that some or all of their content
constitutes requirements of this document. For dated references, only the edition cited applies. For
undated references, the latest edition of the referenced document (including any amendments) applies.
ISO 1514, Paints and varnishes — Standard panels for testing
ISO 2808, Paints and varnishes — Determination of film thickness
ISO 4623-2:2016, Paints and varnishes — Determination of resistance to filiform corrosion — Part 2:
Aluminium substrates
ISO 8044, Corrosion of metals and alloys — Basic terms and definitions
ISO 17872, Paints and varnishes — Guidelines for the introduction of scribe marks through coatings on
metallic panels for corrosion testing
3 Terms and definitions
For the purposes of this document, the terms and definitions given in ISO 8044 and the following apply.
ISO and IEC maintain terminological databases for use in standardization at the following addresses:
—
ISO Online browsing platform: available a
3.1
reference material
material with known test performance
3.2
reference specimen
portion of the reference material (3.1) that is to be exposed with the intention to check the reproducibility
and repeatability of the test results for the test cabinet in use
3.3
test specimen
specific portion of the samples upon which the testing is to be performed
3.4
substitute specimen
specimen made of inert materials (such as plastic or glass) used for the substitute of a test specimen (3.3)
4 Test solution
4.1 General
Instructions for the preparation and use of a neutral sodium chloride solution are given in 4.2 and 4.3.
4.2 Preparation of the sodium chloride solution
Dissolve a sufficient mass of sodium chloride in distilled or deionized water with a conductivity no
higher than 20 μS/cm at 25 °C ± 2 °C to produce a concentration of 50 g/l ± 5 g/l. The sodium chloride
concentration of the sprayed solution collected shall be 50 g/l ± 5 g/l. The specific gravity range for a
50 g/l ± 5 g/l solution is 1,029 to 1,036 at 25 °C.
The sodium chloride shall not contain a mass fraction of the heavy metals of copper (Cu), nickel (Ni) and
lead (Pb) in total more than 0,005 %. It shall not contain a mass fraction of sodium iodide more than
0,1 % and a mass fraction of total impurities more than 0,5 %, calculated for dry salt.
NOTE
Sodium chloride with anti-caking agents can act as corrosion inhibitors or accelerators. A useful
sodium chloride salt grade is a grade named Ph. Eur/USP or JIS, ACS.
4.3 pH adjustment
Adjust the pH of the salt solution so that the pH of the sprayed solution collected within the test cabinet
is 6,5 to 7,2 at 25 °C ± 2 °C. Check the pH using electrometric measurement. Measurements of pH
shall be done using electrode suitable for measuring in weakly buffered sodium chloride solutions in
deionized water. Make any necessary corrections by adding hydrochloric acid, sodium hydroxide or
sodium bicarbonate solution of analytical grade.
NOTE
Possible changes in pH can result from loss of carbon dioxide from the solution when it is sprayed.
Such changes can be avoided by reducing the carbon dioxide content of the solution by, for example, heating it
to a temperature greater than 35 °C before it is placed in the apparatus, or by making the solution from freshly
boiled water.
5 Apparatus
5.1 Component protection
All components in contact with the salt mist spray or the test solution shall be made of, or lined with,
materials which are resistant to corrosion by the test solution and which do not influence the corrosivity
of the sprayed test solution.
The supports for the test specimen shall be constructed such that different substrate types do not
influence each other. It shall also be constructed so that the supports themselves do not influence the
test specimens.
5.2 Exposure equipment
5.2.1 Test cabinet, that meets the conditions of homogeneity and distribution of the spray. Due to the
limited capacity of test cabinets smaller than 0,4 m3, the effect of the loading of the test cabinet on the
distribution of the spray and temperature shall be carefully considered. The solution shall not be sprayed
directly onto test specimens but rather spread throughout the test cabinet so that it falls naturally down
on them. The upper parts of the test cabinet shall be designed so that drops of sprayed solution formed
on its surface do not fall on the specimens being tested.
The size and shape of the test cabinet shall be such that during periods of exposure to salt mist spray,
the collection rate of solution in the test cabinet is within the limits specified in 8.2.
NOTE
A schematic diagram of one possible design of test cabinet and associated apparatus for salt mist
cyclic corrosion testing is shown in Annex A.
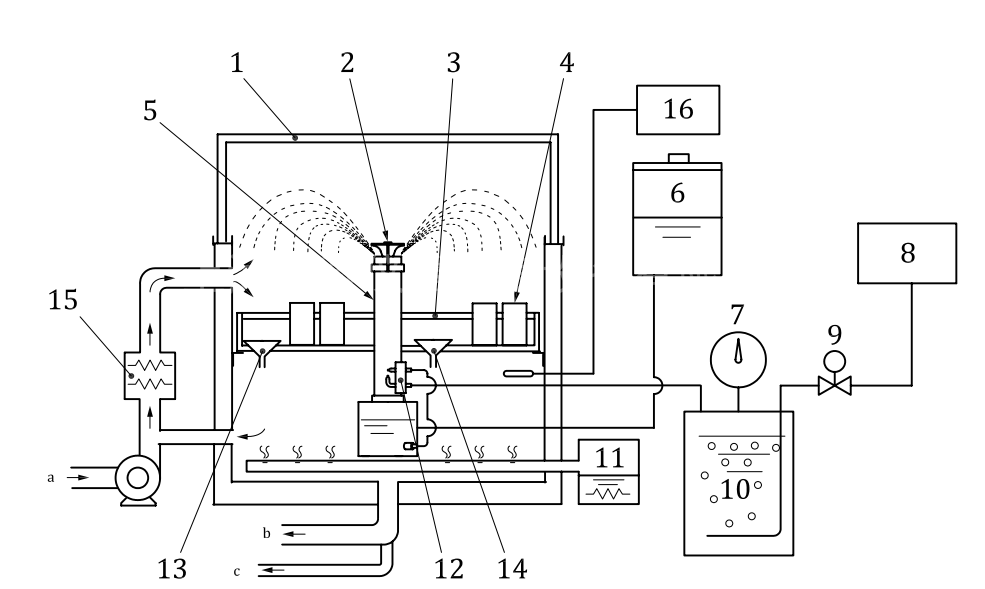
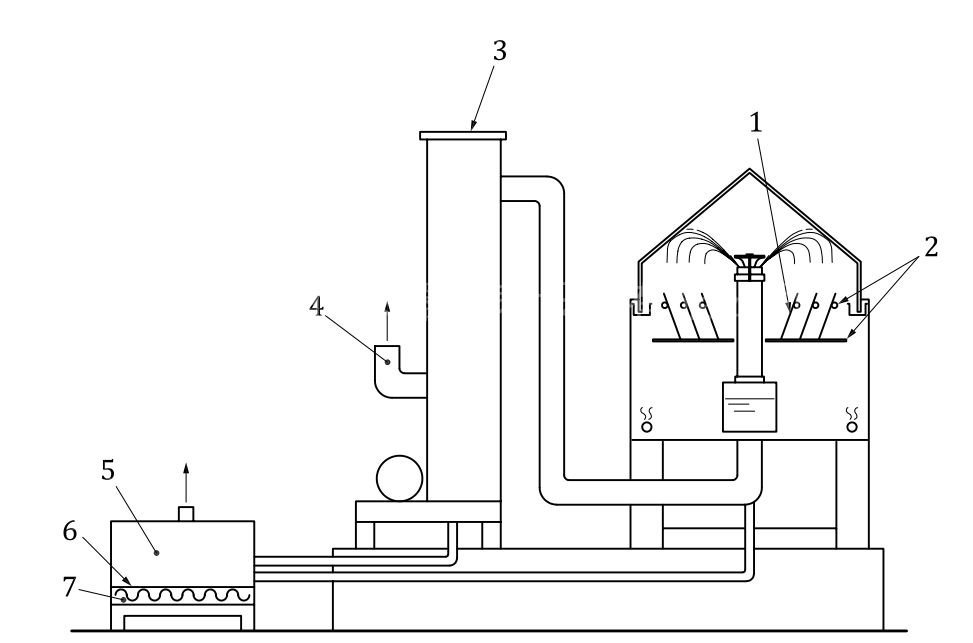
5.2.2 Humidity and temperature control system, that maintains the test cabinet and its contents
at the specified temperature and humidity (see 8.1). The temperature shall be measured at a position at
least 100 mm from walls and radiant heat sources.
5.2.3 Spraying device, for spraying the salt solution during periods of exposure to salt mist spray
comprising a supply of air at controlled pressure, a reservoir containing the solution to be sprayed and
one or more atomizers.
The compressed air supplied to the atomizers shall be passed through a filter to remove all traces
of oil or solid matter and shall be at an overpressure of 70 kPa to 170 kPa. The pressure is typically
98 kPa ± 10 kPa but can vary depending on the type of test cabinet and atomizer used.
5.2.4 Air saturator, consisting of a saturation tower containing hot water at a temperature higher
than that of the test cabinet. In order to prevent evaporation of water from the sprayed droplets, the air
shall be humidified before entering the atomizer, by passage through this tower.
During periods of exposure to the salt mist, the appropriate temperature depends on the pressure used
and on the type of atomizer nozzle and shall be adjusted so that the rate of collection of spray in the test
cabinet and the concentration of the collected spray are kept to within the specified limits (see 8.2). The
level of water shall be maintained automatically to ensure adequate humidification.
The atomizers shall be made of inert material, e.g. glass or plastic materials. Baffles may be used to
prevent direct impact of spray on the test specimens and the use of adjustable baffles is helpful in
obtaining constant distribution of spray within the test cabinet. The level of the salt solution in the
supply tank shall be maintained automatically to ensure constant spray delivery throughout the test.
5.2.5 Collecting devices, at least two, consisting of clean funnels with a collecting area of approximately
80 cm2 made of glass or other chemically inert material, with the stems inserted into graduated cylinders
or other similar containers. The purpose of the collecting devices is to confirm that the collection rate
is within specified limits (see 8.2). They shall be placed in the zone of the test cabinet where the test
specimens are placed, one close to the spray inlet and one remote from an inlet and in such a way that
only spray, and not the liquid falling from specimens or from parts of the test cabinet, is collected.
5.2.6 Air dryer, comprising a heating device and fan to supply dried air of the specified humidity
during “dry” periods (see Table 1).
5.2.7 Exhaust system, by which air is exhausted from the test cabinet. It shall not be influenced by the
back pressure of the atmosphere when the air is released at a point outside the building.
6 Test specimens
6.1 The number and type of test specimens, their shape and their dimensions, shall be selected in
accordance with the specification for the material or product being tested. When not specified, these
parameters shall be mutually agreed between the interested parties. Unless otherwise specified or agreed,
test specimens with an organic coating to be tested shall be made from burnished steel conforming
with ISO 1514, and of approximate dimensions 150 mm × 100 mm × 1 mm. Annex C describes how test
specimens with organic coatings shall be prepared for testing. Annex D gives supplementary information
that shall be supplied, as appropriate, for testing test specimens with organic coatings.
6.2 The test specimens shall be thoroughly cleaned before testing, if not otherwise specified. The
cleaning method employed shall depend on the nature of the material, its surface and the contaminants
and shall not include the use of any abrasives or solvents which may attack the surface of the specimens.
Care shall be taken that test specimens are not re-contaminated after cleaning by careless handling.
6.3 If the test specimens are cut from a larger coated sample, cutting shall be carried out in such a way
that the coating is not damaged in the area adjacent to the cut. Unless otherwise specified, the cut edges
shall be adequately protected by coating them with a suitable material, which remains stable under the
conditions of the test, such as paint, wax or adhesive tape.
7 Arrangement of the test specimens
7.1 The test specimens shall be placed in the test cabinet so that they are not in the direct path of spray
from the atomizer.
7.2 If the test cabinet is not full of test specimens, it is recommended to fill it with inert flat substitute
specimens of the same size as a reference specimen, in order to ensure uniformity of the spray. The
material used shall be plastics, glass, or other inert insulating materials, which would not influence
corrosion of the test specimens being tested.
7.3 The angle at which the surfaces of the test specimens are exposed in the test cabinet is very
important. The specimen shall, in principle, be flat and placed in the test cabinet facing upwards at an
angle as close as possible to 20° to the vertical. This angle shall, in all cases, be within limits 15° to 25°.
In the case of irregular surfaces, e.g. entire components, these limits shall be adhered to as closely as
possible.
7.4 The test specimens shall be arranged so that they do not come into contact with the test cabinet
and so that the surfaces to be tested are exposed to free circulation of spray. The specimens may be placed
at different levels within the test cabinet, as long as the solution does not drip from specimens or their
supports at one level onto other specimens placed below. However, for a new examination, or for tests with
a total duration exceeding 96 h, location permutation of specimens is permitted. In this case, the number
and frequency of the permutations are left to the operator and shall be indicated in the test report.
7.5 The supports for the test specimens shall be made of inert non-metallic material, such as glass,
plastic or suitably coated wood. If it is necessary to suspend specimens, the material used shall not be
metallic but shall be synthetic fibre, cotton thread or another inert insulating material.
8 Operating conditions
8.1
The test conditions are summarized in Table 1.
1 | Salt mist conditions 1) Temperature 2) Salt solution | 35 °C ± 1 °C pH 6,5 to 7,2, salt concentration 50 g/l ± 5 g/l as described in Clause 4
|
2 | “Dry” conditions (The air is purged under dry conditions.) 1) Temperature 2) Relative humidity
| 60 °C ± 1 °C < 30 %
|
3 | “Wet” conditions (Condensation on the test specimens shall not occur under wet conditions.) 1) Temperature 2) Relative humidity
| 50 °C ± 1 °C > 95 %
|
4 | Period and content of a single exposure cycle
| Total period 8 h, as follows: Salt mist spray 2 h “Dry” conditions 4 h “Wet” conditions 2 h (These times include the time for reaching the specified temperature for each condition.) |
5 | Time to reach the specified condition (i.e. period taken for temperature and humidity to reach the specified values once the test condition has begun) | Mist to “Dry” < 30 min “Dry” to “Wet” < 15 min “Wet” to Mist < 30 min (Mist conditions are attained almost instantaneously once this condition begins.)
|
6 | Angle at which test specimens are supported | 20° ± 5° to the vertical
|
NOTE The ± tolerances given are the allowable operational fluctuations, which are defined as the positive and negative deviations from the setting of the sensor at the operational control set point during equilibrium conditions. This does not mean that the set value may vary by plus/minus the amount indicated from the given value.
|
8.2 The test shall not be started until it has been confirmed, with the test cabinet filled to a similar
extent as during the test, that, when the apparatus is operated in the salt mist condition, the collection
rate of solution measured over a period of 24 h of continuous spraying is within the range 1 ml/h to
2 ml/h for a horizontal collecting area of 80 cm2 and that other conditions are as specified. In particular,
the solution collected in each of the collecting devices shall have a sodium chloride concentration of
50 g/l ± 5 g/l and a pH value in the range 6,5 to 7,2.
8.3 A test solution that has been sprayed shall not be re-used.
8.4 During the salt mist conditions of the test, the change from the set pressure shall be
within ± 0,002 5 MPa.
at regular intervals. A suitable method for the evaluation of the corrosivity of the apparatus by use of
reference specimens is described in Annex B.
8.6 During operation, the solution tank shall be covered by a lid to prevent dust or other contaminants
from influencing the solution and to prevent the concentration of sodium chloride and the pH from
fluctuating.
9 Continuity of tests
Tests shall preferably be continued without interruption throughout the test duration. When it
is necessary to interrupt the operation for the removal of specimens for inspection, the period of
interruption should be minimized. In case of interruption for a longer period, its cause, duration and
treatment used shall be stated to the test report.
10 Duration of tests
The period of test shall be as designated by the specification covering the material or product being
tested. When not specified, the period shall be agreed by the interested parties.
Recommended periods of exposure are 30 cycles (240 h), 45 cycles (360 h), 60 cycles (480 h), 90 cycles
(720 h), 180 cycles (1 440 h).
11 Treatment of test specimens after testing
11.1 General
How to treat test specimens after testing should be included in the test specification or material
specification given by the customer. It shall be agreed with the test parties before starting the test.
11.2 Non-organic coated test specimens: metallic and/or inorganic coated
At the end of the test period, remove the test specimens from the test cabinet and allow them to dry
for 0,5 h to 1 h before rinsing, in order to reduce the risk of removing corrosion products. Before they
are examined, carefully remove the residues of spray solution from their surfaces. A suitable method
is to rinse the test specimens gently in clean running tap water, at a temperature not exceeding 40 °C,
and then to dry them immediately in a stream of air, at an overpressure not exceeding 200 kPa and at a
distance of approximately 300 mm.
NOTE
ISO 8407 can be used for treatment of the specimen after the test.
11.3 Organic coated test specimens
11.3.1 Scribed organic coated test specimens
Clean the surface of the organic coated test specimens under running tap water directly after removing
the test specimens out of the test cabinet. A soft sponge may be used to remove dirt and salt rests out
of the scribed area but not to remove evaluable corrosion phenomena. Remove the delaminated area
around the scribe by one of the following methods.
a)
Using a knife. Carefully remove the loose coating using a knife blade held at an angle, positioning
the blade at the interface between the coating and the substrate and forcing the coating away from
the substrate.
b)
Using an adhesive tape.
NOTE
Removing the organic coating (paint coating) depends on the kind of coating (paint) and its behaviour
in wet conditions. If agreed by the interested parties, let the test specimens dry in room atmosphere for 24 h and
then treat them as described under a) and b).
11.3.2 Organic coated but not scribed test specimens
Coated but not scribed test specimens shall be cleaned under running tap water so that corrosion
products and/or corrosion phenomena which have to be evaluated are not influenced by cleaning.
12 Evaluation of results
Many different criteria for the evaluation of the test results may be applied to meet particular
requirements, for example:
a)
appearance after the test;
b)
appearance after removing superficial corrosion products;
c)
number and distribution of corrosion defects, i.e. pits, cracks, blisters, rusting or creep from scribes
in the case of organic coatings be assessed by methods described in ISO 8993 or ISO 10289 and, for
organic coatings, in ISO 4628-1, ISO 4628-2, ISO 4628-3, ISO 4628-4, ISO 4628-5 and ISO 4628-8
(see Annex D);
d)
the time elapsed before the appearance of the first signs of corrosion;
e)
changes in mass (in accordance with ISO 8407);
f)
alteration revealed by micrographic examination;
g)
changes in mechanical properties.
NOTE
It is good engineering practice to define the appropriate criteria in the specification for a coating or a
product to be tested.
13 Test report
The test report shall contain the following information:
a)
reference to this document, i.e. ISO 14993:2018;
b)
type and purity of salt and water used;
c)
description of the test equipment;
d)
description of the material or product tested;
e)
dimensions and shape of the test specimen, and the nature and area of the surface tested;
f)
preparation of the test specimen, including any cleaning treatment applied before testing and any
protection given to edges or other special areas;
g)
known characteristics of any coating, with an indication of the surface, if required;
h)
number of test specimens subjected to the test representing each material or product;
i)
angle at which the tested surfaces were inclined;
j)
temperature and relative humidity in each of the salt mist, “dry” and “wet” conditions during
testing;
k)
the time taken to undergo the transitions from mist to “dry”, “dry” to “wet”, and “wet” to salt mist
conditions during the test;
l)
mist collection rate, salt concentration and pH of the solution collected during the pre-test;
m)
the corrosivity of test determined as, for example, described in Annex B;
n)
the frequency and duration of any interruptions;
o)
the number of cycles or the duration of the test;
p)
the frequency and number of the test specimen location permutation, if required;
q)
the method used to clean the test specimen after testing and any loss resulting from the cleaning
operation and the method used for calibrating this mass loss;
r)
test results (see Clause 12);
s)
if necessary, photographic records and/or descriptions of the appearance of tested specimens;
t)
any deviation from test procedure;
u)
any unusual features observed;
v)
the date of the test
免責聲明
- 凡本網注明“來源:化工儀器網”的所有作品,均為浙江興旺寶明通網絡有限公司-化工儀器網合法擁有版權或有權使用的作品,未經本網授權不得轉載、摘編或利用其它方式使用上述作品。已經本網授權使用作品的,應在授權范圍內使用,并注明“來源:化工儀器網”。違反上述聲明者,本網將追究其相關法律責任。
- 本網轉載并注明自其他來源(非化工儀器網)的作品,目的在于傳遞更多信息,并不代表本網贊同其觀點和對其真實性負責,不承擔此類作品侵權行為的直接責任及連帶責任。其他媒體、網站或個人從本網轉載時,必須保留本網注明的作品第一來源,并自負版權等法律責任。
- 如涉及作品內容、版權等問題,請在作品發表之日起一周內與本網聯系,否則視為放棄相關權利。